Machine Tool
Machine Tool
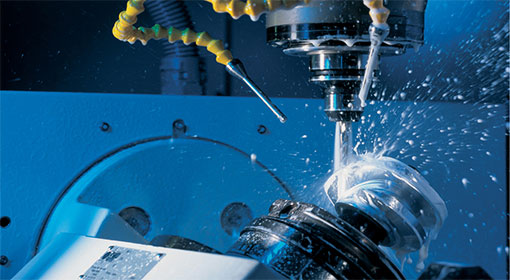
In machine tools, a spindle is a rotating axis of the machine, which often has a shaft at its heart. The shaft itself is called a spindle, but also, in shop-floor practice, the word often is used metonymically to refer to the entire rotary unit, including not only the shaft itself, but its bearings and anything attached to it (chuck, etc.).
A machine tool may have several spindles, such as the headstock and tailstock spindles on a bench lathe. The main spindle is usually the biggest one. References to "the spindle" without further qualification imply the main spindle. Some machine tools that specialize in high-volume mass production have a group of 4, 6, or even more main spindles. These are called multispindle machines. For example, gang drills and many screw machines are multispindle machines. Although a bench lathe has more than one spindle (counting the tailstock), it is not called a multispindle machine; it has one main spindle.
Examples of spindles include
On a lathe (whether wood lathe or metal lathe), the spindle is the heart of the headstock.
In rotating-cutter woodworking machinery, the spindle is the part on which shaped milling cutters are mounted for cutting features (such as rebates, beads, and curves) into mouldings and similar millwork.
Similarly, in rotating-cutter metalworking machine tools (such as milling machines and drill presses), the spindle is the shaft to which the tool (such as a drill bit or milling cutter) is attached (for example, via a chuck).
Varieties of spindles include grinding spindles, electric spindles, machine tool spindles, low-speed spindles, high speed spindles, and more.
Types of Machine Tool Spindles: CNC Machine Spindles, Motorized Spindles, Multi Drill and Tap Head, Box and Cartridge spindles, Gear Driven Spindles, Belt Driven Spindles, Cluster Spindles, and any Specialty Spindles.
Spindle ball bearings are single-row angular contact ball bearings with a contact angle of 15° or 25° that can support load on one side. In respect of their design, their running accuracy and the materials used, they are optimised for highest speed and great bearing capacity.
Previous: Oil drilling
Next: Robotics